Can Excel Replace ERP Automation? Debunking the Myths and Realities
- Azlan Mohamad
- Jul 30, 2023
- 3 min read
Updated: Jul 30, 2023

In today's competitive business landscape, manufacturing, distribution, and warehousing industries require efficient and intelligent systems to manage complex operations, optimize processes, and drive productivity. Two key contenders in this arena are Microsoft Excel and Enterprise Resource Planning (ERP) systems. Both have distinct advantages, but understanding how they fare in critical aspects such as Business Intelligence (BI), Industrial Automation, and Artificial Intelligence (AI) is essential for making informed decisions. Let's delve into their strengths and limitations and explore how they complement each other in these industries.
Microsoft Excel in Manufacturing, Distribution, and Warehousing
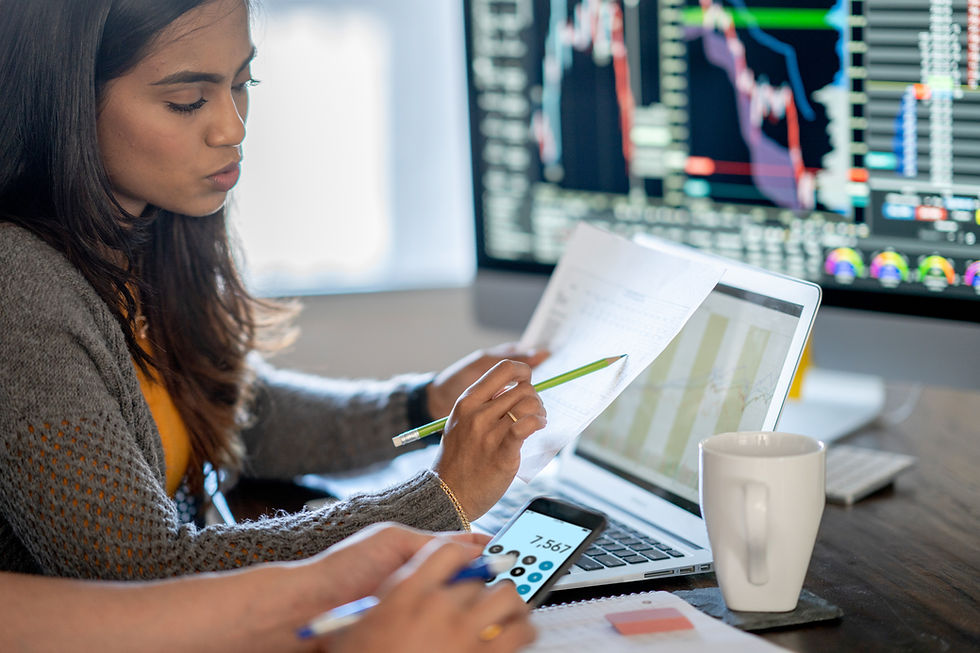
Microsoft Excel, a versatile spreadsheet application, has been a staple tool for data management, analysis, and visualization. Its ease of use and widespread familiarity make it an attractive choice for businesses of all sizes. In manufacturing, distribution, and warehousing, Excel is often utilized for tasks like basic data entry, simple calculations, and generating reports.
Business Intelligence (BI) in Excel: Excel's pivot tables and charts provide basic BI capabilities, allowing users to summarize and visualize data. However, handling large datasets and generating complex visualizations might be challenging for Excel, limiting its analytical potential.
Industrial Automation in Excel: Excel can be integrated with automation scripts and macros to automate repetitive tasks and perform calculations. However, its capabilities might fall short in managing the complexity of industrial automation processes in these industries.
Artificial Intelligence (AI) in Excel: With the integration of AI-powered add-ins or custom scripts, Excel can enable some level of predictive analysis and automated insights. However, implementing advanced AI algorithms may be limited due to Excel's constraints.
ERP System for Manufacturing, Distribution, and Warehousing

ERP systems are purpose-built solutions designed to streamline operations and improve efficiency across multiple business functions. In the context of manufacturing, distribution, and warehousing, ERP systems offer a comprehensive suite of tools and functionalities tailored to address specific industry requirements.
Business Intelligence (BI) in ERP: ERP systems excel in BI, offering robust analytics, reporting, and data visualization capabilities. They provide real-time access to critical information, empowering decision-makers with actionable insights for strategic planning and operational improvements.
Industrial Automation in ERP: ERP systems integrate with industrial automation systems, enabling real-time data collection and analysis. This integration enhances production planning, inventory management, and quality control, contributing to increased productivity and efficiency.
Artificial Intelligence (AI) in ERP: Many modern ERP systems integrate AI technologies for predictive analytics, demand forecasting, and intelligent process automation. AI-powered ERP solutions provide a significant competitive advantage, optimizing operations and reducing manual efforts.
Complementing Excel with ERP: A Winning Combination
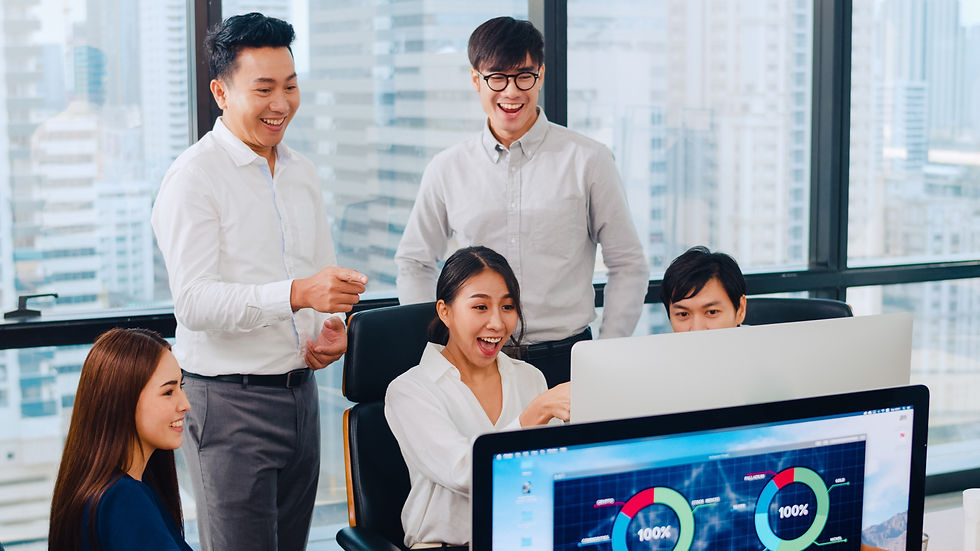
While Excel can perform basic data analysis and automation tasks, it is no match for the comprehensive capabilities of an ERP system in manufacturing, distribution, and warehousing industries. The key is to leverage the strengths of both Excel and ERP to create a synergistic and powerful solution.
Business Intelligence (BI) and AI with Excel and ERP: Excel can complement ERP by providing ad hoc reporting and visualization on specific datasets, while ERP brings sophisticated BI tools to analyze data on a larger scale. The integration of AI-powered add-ins with both Excel and ERP enhances predictive analytics and automated insights.
Industrial Automation with Excel and ERP: Excel can act as a supplementary data collection tool for small-scale automation processes, while ERP facilitates seamless integration with industrial automation systems for real-time data monitoring and analysis.
Can Excel Replace ERP Automation?
While Excel's automation capabilities are valuable for smaller tasks, it cannot fully replace ERP automation in manufacturing, distribution, and warehousing. ERP automation is designed to handle complex and interconnected business processes across departments, providing scalability, data integrity, and real-time updates that Excel alone cannot achieve.

THE VERDICT
In the fast-paced and data-driven world of manufacturing, distribution, and warehousing, the combination of Microsoft Excel and an ERP Automation System is unbeatable. While Excel provides user-friendly data manipulation and basic automation, Automated ERP systems offer sophisticated Business Intelligence, Industrial Automation, and Artificial Intelligence tools that drive efficiency, optimize operations, and foster data-driven decision-making. Integrating Excel and ERP creates a powerful ecosystem that allows businesses to adapt, innovate, and thrive in the ever-evolving landscape of modern industries.
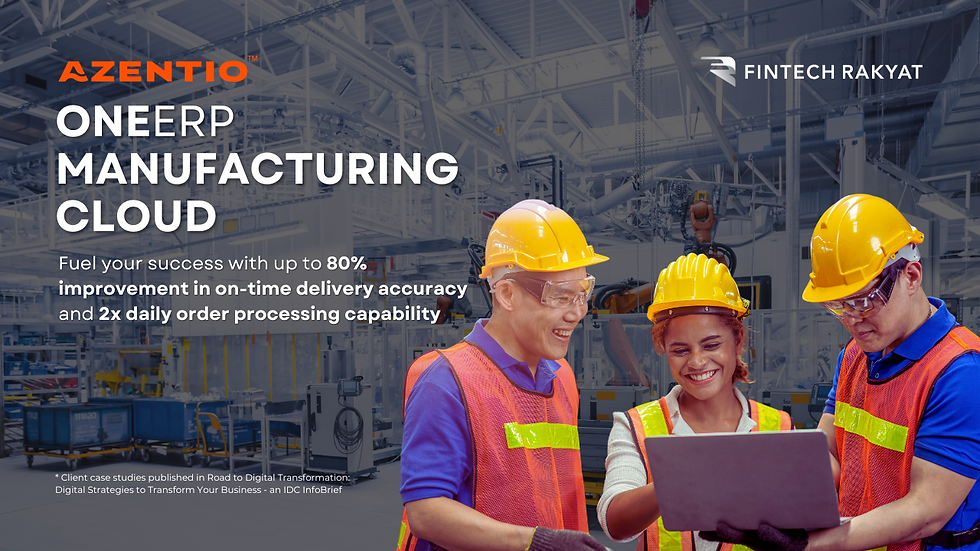
FINTECH RAKYAT is a Business Process Automation (BPA) Technology Consultancy based in Kuala Lumpur, Malaysia. We implement, support and manage software & hardware, covering our client's software journey from IT consulting to business automation and localized support, helping them avoid implementation failures and high opportunity costs, so they can focus on innovation & growth.
Save on your next ERP Investment with FINTECH RAKYAT, the Preferred Business Automation and Digital Transformation (DX) Specialist.
Ask us how and get a free 60mins consultation!
+603 2935 9804 | sales@fintechrakyat.com
コメント